MARIE CURIE ACTIONS
Project H2020-MSCA-IF-2015 – GA - 705944
High Performance Seasonal Solar Energy Latent Heat Thermal Storage Using
Low Grade, Low Melting Temperature Metallic (THERMOSTALL)
Project duration: 24 months (2016-2018); Grant value: € 195k
Funded by EUROPEAN COMMISSION Research Executive Agency
PI: Prof. K Mahkamov; MC Research Fellow: Dr. Carolina Costa;
Aim and Objectives
Energy storage
technologies have long been a subject of great interest to both academia and
industry. The aim of this project is to develop a novel, cost effective and
high performance Latent Heat Thermal Energy Storage System (LHTESS) for
seasonal accumulation of solar energy in increased quantities.
The major barrier for
currently used organic, salt and salt hydrates based Phase Change Materials is
their very low thermal conductivity coefficient and density, which results in
the relatively large volumes of storage systems and difficulties in achieving
the necessary rates of thermal energy re-charge and discharge, even when using
advanced heat exchangers.
The new approach to
overcome the above issues is the deployment of low grade, low
melting temperature metallic alloys (ELMTAs). The ELMTAs are currently produced
for application in other industrial sectors (e.g. electronics) and have not
been actively considered for the thermal energy accumulation with the exception
of very limited studies. Their heat conduction is two orders of magnitude
greater than that of conventional PCMs and they are stable and can provide the thermal
storage capacity which is 2-3 times greater per unit of volume due to the
greater densities.
The project consists of
both theoretical and experimental investigations. A range of low grade ELMTAs
for application in LHTESS have been selected and their thermophysical
properties are being studied using Differential Scanning Calorimetry and
thermal conductivity analysis. Thermal cycling tests of such alloys are also being
conducted.
Numerical investigations
of heat transfer and flow in the LHTESS with ELMTAs will be performed.
Experimental studies of heat transfer and flow in a laboratory prototype of the
LHTESS with ELMTAs will be conducted. As outcomes of investigations,
dimensionless heat transfer correlations will be derived and design
recommendations for a practical solar energy seasonal LHTESS with the low grade
ELMTA will be produced for a project industrial partner.
Brief description of Literature analysis
Through literature
analysis shows that here is no a clear consensus about the use of metallic materials
as PCMs (MPCMs) for LHTES. The low thermal conductivity of the common PCMs,
leads to the need for bigger heat exchange surfaces or embedding metal or
graphite/carbon structures into the PCMs to enhance their performance. Such the
approach negatively affects the feasibility of LHTES [1,
2].
On the other hand, metallic PCMs (MPCMs)
have a significant advantage in thermal
conductivity and this parameter does not require enhancing [3-8]. However, there are a number of
research works [9-13] which highlight the low heat of fusion per unit weight [4,
6-8, 12, 14], high degree of sub-cooling and their relatively high cost, compared to
that of more conventional PCMs. To date, metal alloys have not been endorsed as
effective PCMs although they have also some additional advantages such as high
density, low corrosiveness and small
volume change during melting and solidification [17].
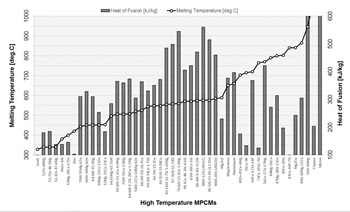
For high temperature
applications aluminium alloys were investigated in [15] as potential PCMs (>300 °C) because of
their high latent heat and good thermal stability.
Information on the lowest
reported values of the heat of fusion for high
temperature MPCMs is summarised in Fig. 1. It can be seen that eutectic
aluminium alloys have the highest heat
of fusion in the group considered. With regard to the cost and availability of the materials, prices for Mg, Zn, Si and Al are approximately
between 2 and 3 $/kg and these materials are widely used in various industrial
applications [16].
For the mid- temperature
range (between 48 and 124 °C), metals with the low melting temperature or
alloys based on elements such as Bi, Pb, Sn, Cd, In, Ga, Zn, Sb etc., are
available. Low-melting-point alloys are extensively used in the fields of materials
processing, electronics, electrical automatic control, continuous casting
simulation, welding etc. [17, 18]. Bismuth is one
of the major components of many fusible alloys, which strongly influence the value
of melting point, and has the unique
characteristic, namely it expands during
solidification process [19]. Summary of
information on melting temperatures and heat of fusion of some mid-temperature
MPCMs, investigated in a number of studies, is presented in Fig. 2.
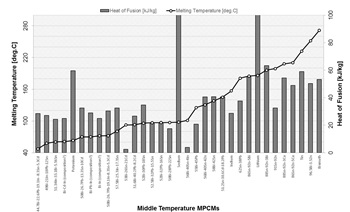
Many of alloys, which
could be deployed in the mid-temperature range, contain harmful elements, such
as lead (Pb). Lead is considered as one of the top 17 chemicals, harmful for
human life and environment. This is highlighted by the Environmental Protection
Agency (EPA) and the European Union's RoHS (Restriction of Hazardous Substances
in Electrical and Electronic Equipment). Therefore, lead containing materials
should be treated with special
protection measures put in place.
Lead-free solders
were studied in [20-31] with relevant
databases have been created [32-34]. Three most
frequently referenced lead-free alloys to substitute the Pb-Sn eutectic composition
solder are Sn–Ag–Cu (near eutectic), Sn–Zn (eutectic) and Sn–Bi (eutectic) composites.
At present, the Sn– (3–4) wt% Ag–(0.5–0.9) wt% Cu alloy
is preferred for application in soldering [21]. This is due to a
number of factors, that affect the soldering process, namely mechanical properties,
melting point, cost, availability and wetting property. Furthermore, Pb-free solders are used because of their cost competitiveness. in order to maintain acceptable costs of
production in electronic industry. On elemental basis, Pb and Zn are the
cheapest metals, whilst In is more
expensive than Ag.
At the low-temperature
range (about 40 °C), liquid metals or low melting point alloys have been
studied and used for diverse applications, mainly as thermal management in
electronic devices. Room temperature liquid metals seem to meet most of the
requirements for meeting thermal comfort requirements [6]. Fig. 3 presents summary of gathered information on the melting temperatures and heat of
fusion for such the low-temperature MPCMs.
Selected ELMTAs and their Characterization
Eight commercially
available ELMTAs were selected as potential candidates as PCMs for the seasonal
thermal storage (see Fig. 4):
Name
|
Chemical
composition
|
Melting Point
|
Alloy 158F
|
50Bi-26.7Pb-13.3Sn-10Cd
|
70
|
Alloy 174F
|
57Bi-26In-17Sn (lead-free)
|
79
|
Alloy 203F
|
52.5Bi- 32Pb-15.5Sn
|
95
|
Alloy 281F
|
58.0Bi- 42.0Sn (lead-free)
|
138
|
Alloy 62S
|
62.5Sn- 36.1Pb- 1.4Ag
|
179
|
Alloy 63/37
|
63.0Sn- 37.0Pb
|
183
|
Alloy 96S
|
96.5Sn- 3.5Ag (lead-free)
|
221
|
Alloy 99C
|
99.3Sn- 0.7Cu
|
227
|
Alloys listed above are widely
used commercially in soldering processes and are described in the standard specifications for Low Melting
Point Alloys ASTM B774 [35] (<183 °C) and in Soft solder alloys BS-EN-ISO 9453 (<450 °C) [36]. The impurity
level in these commercial alloys is <0.15
wt.%.
Differential Scanning
Calorimetry analysis was used to determine the latent heat, phase change
temperature and heat capacity of the selected ELMTAs as a function of the
temperature. DSC measurements were
performed in argon gas environment using a Setaram EVO131 Differential Scanning
Calorimeter. The DSC calibration was performed following the
Standard Test Method ASTM B1269 [37]. During the
measurements the DSC apparatus was purged with argon, all the weigh
measurements were carried out with the
accuracy of ± 0.01 mg. The calorimeter was calibrated with the melting point and enthalpy of
fusion for high-purity Sn. The ELMATs specimens were placed in aluminium
crucibles (30 mm)
and samples were thermally cycled 2-3 times with the heating and cooling rates
of 2 K/min. The maximum heating temperatures were set about 50 K higher than
the melting temperatures.
The above data obtained
for ELMTAs from literature review and experimental characterisation of thermal
properties was saved as database.
Figures 5 and 6 show samples
of results from DSC measurements for one
of the selected ELMATs, namely Alloy 158F. Bolton 158F and Roto 158F are the
same alloy, supplied by two different companies. Heating rate used in
measurements was 5 K/min.
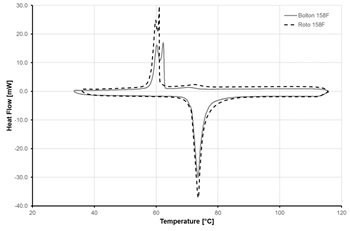
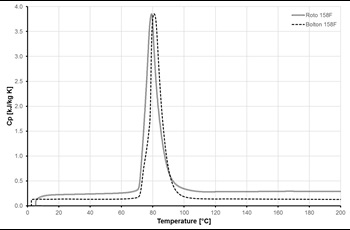
Fig. 5 demonstrates the
significant temperature difference in the melting and crystallisation processes
(75 and 60 °C, respectively) which is caused by the slow rate of crystal
structure formation in metallic alloys.
The variation of the specific
heat capacity of the Alloy 158F as function of temperature, is shown in Fig.6
(the heating rate used was 20 K/min). This diagram indicates that the phase change
process takes place in the temperature range between 70 and 90 °C.
Most of MPCMs may have
this considerable temperature difference between melting and solidification
temperatures, which should be taken into account during thermal storage system
design and exploitation phases.
Overall metallic alloys
provide much superior performance in terms of heat charging and discharging
times. Figs. 7 and 8 below show comparison of this performance during
discharging process (solidification) for Tin and Solar Salt based thermal
storages with the same capacity. It can be clearly seen that during the same
period of time significantly more heat
was delivered to the user when the storage was metallic alloy based.
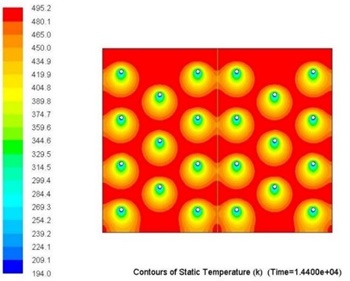
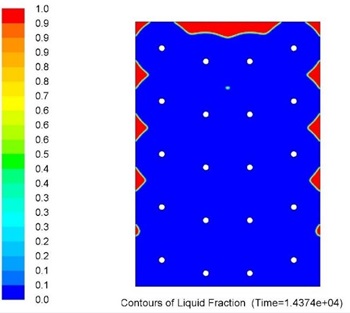
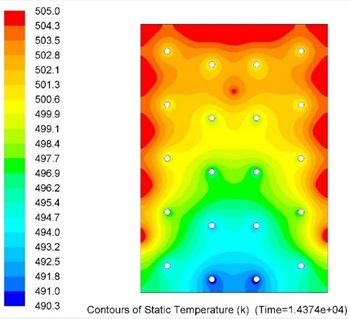
Current work
Several alloys were selected
for further investigations to determine the influence of higher levels of
impurity (>1wt.%) on their thermophysical properties as MPCMs.
Presently, measurements of the thermal conductivity as
a function of temperature for the selected MPCMS is ongoing.
The short-term
thermal stability experiments (100 cycles) using the DSC technique are being
run.
Numerical and experimental
investigations of heat transfer and flow in the laboratory prototype of LHTESS
with ELMTAs for deriving heat transfer correlations.
Practical Applications
Results obtained will be
used in the development of a novel
effective Solar Thermal Energy Storage systems for a small solar power plant
Innova MicroSolar - (Project 723596 - H2020-EE-2016-2017/H2020-EE-2016-RIA-IA, 2016-2020).
Additionally, outcomes
will be used in R&D activities of the industrial partner in THERMOSTALL
Project.
References
[1] F. Agyenim, N. Hewitt, P. Eames, and
M. Smyth, "A review of materials, heat transfer and phase change problem
formulation for latent heat thermal energy storage systems (LHTESS)," Renewable and Sustainable Energy Reviews, vol.
14, pp. 615-628, 2010.
[2] J. P. Kotzé,
"Thermal energy storage in metallic phase change materials," Doctor
of Philosophy, Faculty of Engineering, Stellenbosch University, 2014.
[3] M. M. Kenisarin,
"High-temperature phase change materials for thermal energy storage," Renewable and Sustainable Energy Reviews, vol. 14, pp. 955-970, 2010.
[4] H. Ge and J. Liu,
"Phase change effect of low melting point metal for an automatic cooling
of USB flash memory," in Frontiers
in Energy vol. 6, ed, 2012, pp. 207-209.
[5] M. Liu, W. Saman,
and F. Bruno, "Review on storage materials and thermal performance
enhancement techniques for high temperature phase change thermal storage
systems," Renewable and Sustainable
Energy Reviews, vol. 16, pp. 2118-2132, 2012.
[6] H. Ge, H. Li, S.
Mei, and J. Liu, "Low melting point liquid metal as a new class of phase
change material: An emerging frontier in energy area," Renewable and Sustainable Energy Reviews, vol.
21, pp. 331-346, 2013.
[7] S. A. Mohamed, F.
A. Al-Sulaiman, N. I. Ibrahim, M. H. Zahir, A. Al-Ahmed, R. Saidur, et al., "A review on current
status and challenges of inorganic phase change materials for thermal energy
storage systems," Renewable and
Sustainable Energy Reviews, vol. 70, pp. 1072-1089, 2017.
[8] B. Cárdenas and N.
León, "High temperature latent heat thermal energy storage: Phase change
materials, design considerations and performance enhancement techniques," Renewable and Sustainable Energy Reviews, vol.
27, pp. 724-737, 2013.
[9] M. M. Farid, A. M.
Khudhair, S. A. K. Razack, and S. Al-Hallaj, "A review on phase change
energy storage: materials and applications," Energy Conversion and Management, vol. 45, pp. 1597-1615, 2004.
[10] A. M. Khudhair and
M. M. Farid, "A review on energy conservation in building applications
with thermal storage by latent heat using phase change materials," Energy Conversion and Management, vol.
45, pp. 263-275, 2004.
[11] A. Gil, M. Medrano,
I. Martorell, A. Lázaro, P. Dolado, B. Zalba,
et al., "State of the art on high temperature thermal energy storage
for power generation. Part 1—Concepts, materials and modellization," Renewable and Sustainable Energy Reviews, vol.
14, pp. 31-55, 2010.
[12] A. Sharma, V. V.
Tyagi, C. R. Chen, and D. Buddhi, "Review on thermal energy storage with
phase change materials and applications," Renewable and Sustainable Energy Reviews, vol. 13, pp. 318-345,
2009.
[13] N. Soares, J. J.
Costa, A. R. Gaspar, and P. Santos, "Review of passive PCM latent heat
thermal energy storage systems towards buildings’ energy efficiency," Energy and Buildings, vol. 59, pp.
82-103, 2013.
[14] T. Khadiran, M. Z.
Hussein, Z. Zainal, and R. Rusli, "Advanced energy storage materials for
building applications and their thermal performance characterization: A
review," Renewable and Sustainable
Energy Reviews, vol. 57, pp. 916-928, 2016.
[15] J. Q. Sun, R. Y.
Zhang, Z. P. Liu, and G. H. Lu, "Thermal reliability test of Al–34%Mg–6%Zn
alloy as latent heat storage material and corrosion of metal with respect to
thermal cycling," Energy Conversion
and Management, vol. 48, pp. 619-624, 2007.
[16] P.
Blanco-Rodríguez, J. Rodríguez-Aseguinolaza, E. Risueño, and M. Tello,
"Thermophysical characterization of Mg–51%Zn eutectic metal alloy: A phase
change material for thermal energy storage in direct steam generation applications," Energy, vol. 72, pp. 414-420, 2014.
[17] K. Zhou, Z. Tang,
Y. Lu, T. Wang, H. Wang, and T. Li, "Composition, Microstructure, Phase
Constitution and Fundamental Physicochemical Properties of Low-Melting-Point
Multi-Component Eutectic Alloys," Journal
of Materials Science & Technology, vol. 33, pp. 131-154, 2017.
[18] Z. Mei, H. A.
Holder, and H. A. V. Plas. (1996) Low-Temperature Solders. Hewlett-Packard Journal.
[19] I. Corporation,
"How to Use Fusible Alloys," INDIUM Corporation.
[20] M. Abtew and G.
Selvaduray, "Lead-Free Solders in Microelectronics," Master Science and Engineering, vol. 27,
pp. 95-141, 2000.
[21] K. Suganuma,
"Advances in lead-free electronics soldering," Current Opinion in Solid State and Materials Science, vol. 5, pp.
55–64, 2001.
[22] H. MAVOORI, A. G.
RAMIREZ, and S. JIN, "Lead-Free Universal Solders for Optical and
Electronic Devices," Journal of
ELECTRONIC MATERIALS, vol. 31, 2002.
[23] D. T. Siewert, D.
S. Liu, D. D. R. Smith, and M. J. C. Madeni, "Properties of Lead-Free
Solders," NIST2002.
[24] F. S. Mhiaoui,
"Physical properties of lead free solders in liquid and solid state,"
doctor rerum naturalium, Technischen Universität Chemnitz, 2007.
[25] C. Handwerker, U.
Kattner, M. Gaithersburg, K.-W. Moon, and M. Gaithersburg, "Chapter 2:
Fundamental Properties of Pb-Free Solder Alloys," in Lead-Free Soldering, ed, 2007.
[26] A. A. El-Daly, Y.
Swilem, M. H. Makled, M. G. El-Shaarawy, and A. M. Abdraboh, "Thermal and
mechanical properties of Sn–Zn–Bi lead-free solder alloys," Journal of Alloys and Compounds, vol.
484, pp. 134-142, 2009.
[27] M. Palcut,
J.Sopoušek, L. Trnková, M. Turňa, E.Hodúlová, J. Janovec, et al., "Thermal analysis of selected tin-based lead-free
solder alloys," Kovove Mater., vol.
47, pp. 43-50, 2009.
[28] Yucai Hu, Fengjing
Cao, Fangxiao Li, G. Ni, and a. X. Cui, "RESEARCH PROGRESS ON LEAD-FREE
SOLDERS," 150 Rev. Adv. Mater. Sci., vol. 29, pp. 150-155, 2011.
[29] A. A. El-Daly, A.
E. Hammad, G. S. Al-Ganainy, and A. A. Ibrahiem, "Design of lead-free
candidate alloys for low-temperature soldering applications based on the
hypoeutectic Sn–6.5Zn alloy," Materials
& Design (1980-2015), vol. 56, pp. 594-603, 2014.
[30] Y. Shu, K.
Rajathurai, F. Gao, Q. Cui, and Z. Gu, "Synthesis and thermal properties
of low melting temperature tin/indium (Sn/In) lead-free nanosolders and their
melting behavior in a vapor flux," Journal
of Alloys and Compounds, vol. 626, pp. 391-400, 2015.
[31] A. A. El-Daly, A.
M. El-Taher, and S. Gouda, "Development of new multicomponent Sn–Ag–Cu–Bi
lead-free solders for low-cost commercial electronic assembly," Journal of Alloys and Compounds, vol.
627, pp. 268-275, 2015.
[32] Z. Moser, W.
Gąsior, A. Dębski, and J. Pstruś, SURDAT:
DATABASE OF LEAD - FREE SOLDERING MATERIALS. Kraków, 200.
[33] M. C. Schmetterer,
P. A. Mikula, and P. H. Ipser, "DATABASE FOR PROPERTIES OF LEAD-FREE
SOLDER ALLOYS," 2006.
[34] W. Gąsior, Z.
Moser, A. Dębski, and T. Siewert, "Integration of the NIST and SURDAT
Databases on Physical Properties of Lead-Free Solder Alloys," International Journal of Thermophysics, vol.
31, pp. 502-512, 2010.
[35] ASTM, "ASTM B
774 – 00: Low Melting Point Alloys (Standard)," ed, 2000.
[36] BS, "BS EN
29453-1994: Soft solder alloys — Chemical compositions and forms
(Standard)," ed, 1994.
[37] ASTM, "ASTM
E1269: Standard Test Method for Determining Specific Heat Capacity by
Differential Scanning Calorimetry," ed.
Contacts
Emails: khamid.mahkamov@northumbria.ac.uk Phone: + 44 191 243 7510
carolina.costa@northumbria.ac.uk Phone: + 44 191 243 7649